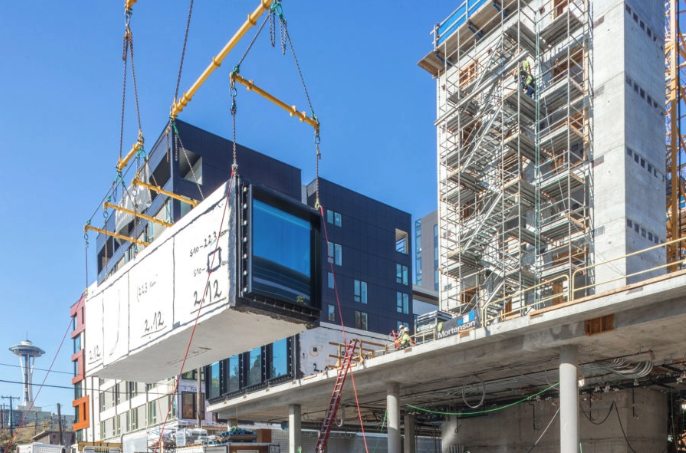
At COR3, we’re always looking toward the future of architecture and design–particularly when it comes to making building processes more efficient, sustainable, and adaptable. One innovation that has been growing in popularity since 2020 is modular construction. For the uninitiated, modular construction is when different parts of a building are constructed offsite, and later assembled at the construction site.
Modular construction reduces construction time since modules can be built simultaneously with site preparation. This significantly reduces the environmental impact in some cases. Off-site construction means less waste and less disturbance to the construction site surroundings.
Sustainability is another major advantage. Modular builds are often more energy-efficient, with better-controlled manufacturing processes leading to tighter fittings and better insulation (SOURCE). Additionally, modular building enables quality control because elements are built in a factory where temperature, light, and humidity are controlled.
It isn’t all sunshine and rainbows when it comes to modular construction, though. One of the key challenges with this concept is transportation logistics. Prefab products are bulky by nature and rely on clever steps to get them from point A to point B. And, like many industries disrupted by supply chain challenges particularly during the pandemic, modular construction is vulnerable to acquisition glitches.
At COR3, we are most intrigued by examples of modular construction in hotels. While we have not yet worked on a project that incorporates this concept of design, we have seen modular elements that arrive at a construction site so complete that art is already on the wall and furniture placed on the floor. (Can you imagine how much shrink wrap it must take to hold everything in place?)
The trend started with lower cost chains but advancements in technology have allowed further customization and creativity. The result is far quicker construction times–for example, in Yellowstone National Park, three modular hotels in a $90 million project were built in six months compared to the 30 months it would have taken for traditional construction (SOURCE.)
Cruise ships are another great example of modular construction These ships are essentially mini-cities on the ocean, and they’re often built like giant LEGO sets. “Blocks” or “modules” are pre-assembled in a shipyard, then lifted into place and welded together to form the complete structure of the ship.
Prefab structures are not a completely new idea. In 1908, gold prospectors were able to order homes in kit form by mail order in the United States, allowing them to move around and quickly construct accommodation wherever needed. In shipbuilding, prefabrication techniques were employed to quickly build warships in World War II, bringing the production time of those ships down from roughly 8 months to mere weeks (SOURCE).
Thanks to advancements in technology and materials, modular buildings can be as aesthetically pleasing and durable as traditionally constructed ones. This method also allows for greater flexibility and scalability in design, making it easier to adapt to changing needs and environments.
We’re excited about the possibilities modular construction brings to our projects, especially in terms of sustainability, efficiency, and innovation. After all, we’re not just building for today–we’re building for the future.